效率管理
致力于辅导本土企业的TPM管理、5S/6S/7S管理、品质管理、供应链管理、成本管理、企业文化等模块的综合管理
生产效率是制作性企业赖以生存之根本,他同品质、成本、交期、士气、安全一起被称为生产管理六大任务,因此生产效率的提升是每个生产管理者必备的能力之一!

【项目描述】
您的企业是否存在:效率低下,订单不稳、设备故障、人员加班、成本控制等等问题。
如何让现场得到有效的改善,逐步提升效率与降低成本,减少与消除现场浪费呢?
GTPM效率改善管理咨询能帮助企业解决以生产现场 管理一系列问题。

GTPM效率改善管理通过分阶段展开“生产布局优化改善”、“标准工时建立”、“动作浪费改善”、“生产线平衡率改善”、“八大浪费改善”、“快速换模改善(SMED)”、“设备综合效率管理”等活动,使人员效率和设备效率最大化,通过改善使生存作业更加高效、轻松安全;生存设备更加精确、更加快速、产能更大。
【推行效果】
有形效果:
作业人员掌握独立或集体共同提高30%以上的生产效率;
有利于消减不必要的动作浪费,从而缩短作业时间40~70%;
提高作业员及设备的工作效率,减少工序时间达40%,真正实现一个流;
建立异常信息标准,提高设备效率60%以上。
无形效果:
有利于养成好的习惯;
提升改善的技能;
各小组经常地进行现场改善,能提升团队凝聚力。
【成功条件】
1、老板(或决策者)改革的意志坚定;
2、人财物的保障充分;
3、对顾问师的授权充分;
4、公司高层对浪费的认识、浪费的意识深刻、各个部门积极配合;
5、公司领导的重视,合格适当、训练有素的作业人员;
6、企业正确认识内外作业,内部作业转化为外部作业,内外作业进行优化;
7、增加设备信息收集和分析的工作量,投入异常对策的实施的相关资源。

【合作流程】
如您确有合作意愿,我们将整个合作过程划分为7个步骤,分别为:

确认合作、首期付款成功、远程发送启动文件、技术部远程指导准备事项、确认辅导日期和顾问师行程、顾问师现场辅导、后期验收。
【实施周期】
持续推行1-2年时间
【推行内容】
1、“生产布局优化改善”
2、“标准工时建立”
3、“动作浪费改善”
4、“生产线平衡率改善”
5、“八大浪费改善”
6、“快速换模改善”
7、“设备综合效率管理”
(不限于以上项目服务内容)

【成功案例】
佛山**机械制造有限公司——“生产布局优化改善”实例
(1)实施背景
伴随推力杆车间设备和工艺的逐步提升,但对厂内的生产物流系统、车间的总体布局、各车间内的物流设施从未做过详尽的、系统的规划和设计,从而制约整个生产效率的提高。
(2)现状解析
通过对现有的设备布局及物料流动绘制推力杆车间布局图如下:
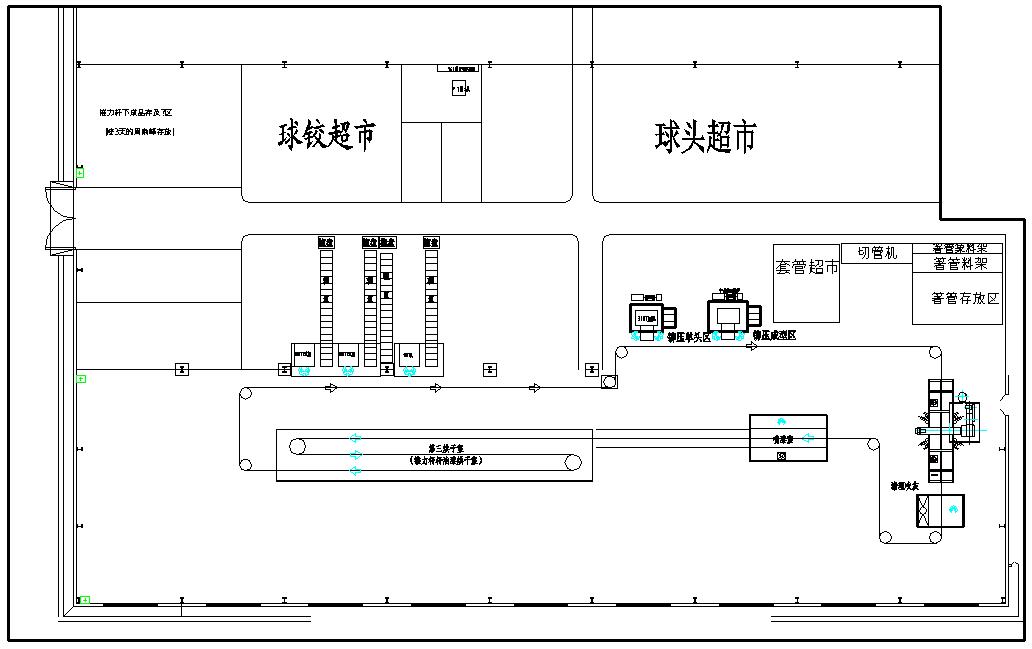
根据区域布局图结合生产情况用鱼骨图形式分析如下:
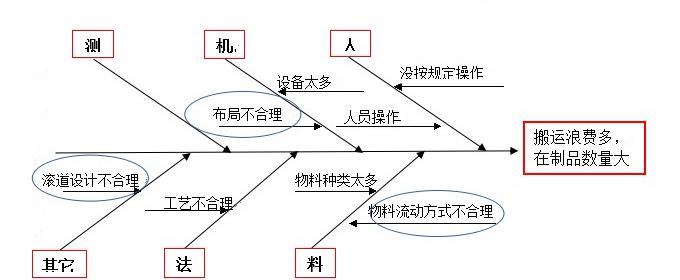
对策确定及实施
通过以上分析,根据布局优化原则,我们针对推力杆生产车间不合理方面主要进行如下改进:
①布局不合理:根据员工操作便利,对切管机位置调整和套管滚道设计;、根据最短距离原则,将球铰压装机位置调整与传送带平行。
②物流流方式不合理:在铆接工序之间,增加推力杆滚道,实现工序间物料衔接;
③滚道设计不合理:根据I/O一致节约物流空间,合理利用空间原则, 取消原有的4条滚道传送线,引进自动传送带。
具体车间布局优化调整效果图如下:
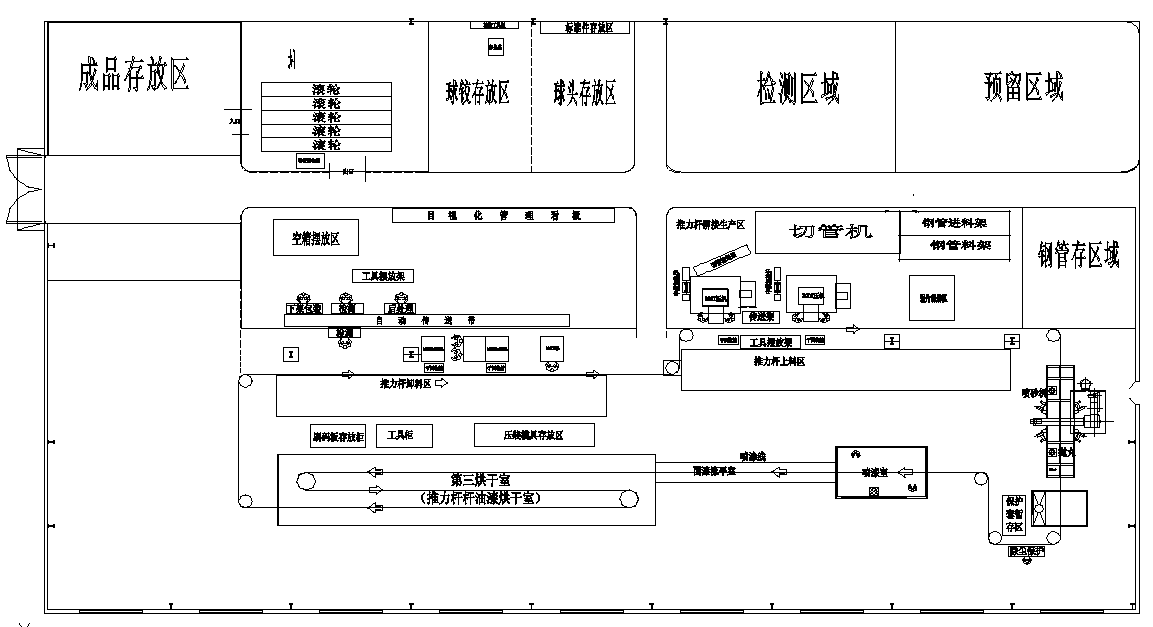
(4)综合效果
①库存方面:通过工序之间输送架的引进及设备布局调整,实现推力杆生产线的单件流生产,生产节拍控制在30S,套管在制品降为10根。
②生产周期:通过优化各工序的物流通道,减少搬运时间,使整个工序生产时间从原有349.5s降低至272.5s,生产周期缩短了77s。
③人员方面:通过对压装机位置调整及后处理自动传送带的引进,使整个工序从22人降至13人,劳动效率提高了59%。
我猜您现在可能存在如下疑问:
- 你们能做什么?
- 需要多少钱?
- 需要多久?
- 我需要做什么?
- 需要提供什么资料?
- 售后服务怎么样?
同样的问题每个人侧重点不同,很难有标准的答案;请认真填写表单信息或直接在线联系,我们会给您最合适的答案!