生产布局优化改善
【通用名称】 一个流生产模式/布局设计
【项目描述】
生产布局优化改善指通过分析决定设备及工序的位置或保管场地等与生产相关的位置设计,帮助客户在达成目标(QCD),满足客户需求的前提下做到有效利用人员、面积,削减在库,推进多能工化。
【项目特点】
简单实效,通过布局优化改善快速实现现场变革。
【推行效果】
简化加工过程,有效地利用人员、设备、空间和能源;
最大限度地减少物料搬运;
缩短生产周期;
力求投资最低;
为职工提供方便、舒适、安全和职业卫生的条件。
【适用企业】
适用于任何实体企业。
【合作流程】
如您确有合作意愿,我们将整个合作过程划分为7个步骤,分别为:

【实施周期】2-6个月
【成功案例】
佛山**机械制造有限公司——“生产布局优化改善”实例
(1)实施背景
伴随推力杆车间设备和工艺的逐步提升,但对厂内的生产物流系统、车间的总体布局、各车间内的物流设施从未做过详尽的、系统的规划和设计,从而制约整个生产效率的提高。
(2)现状解析
通过对现有的设备布局及物料流动绘制推力杆车间布局图如下:
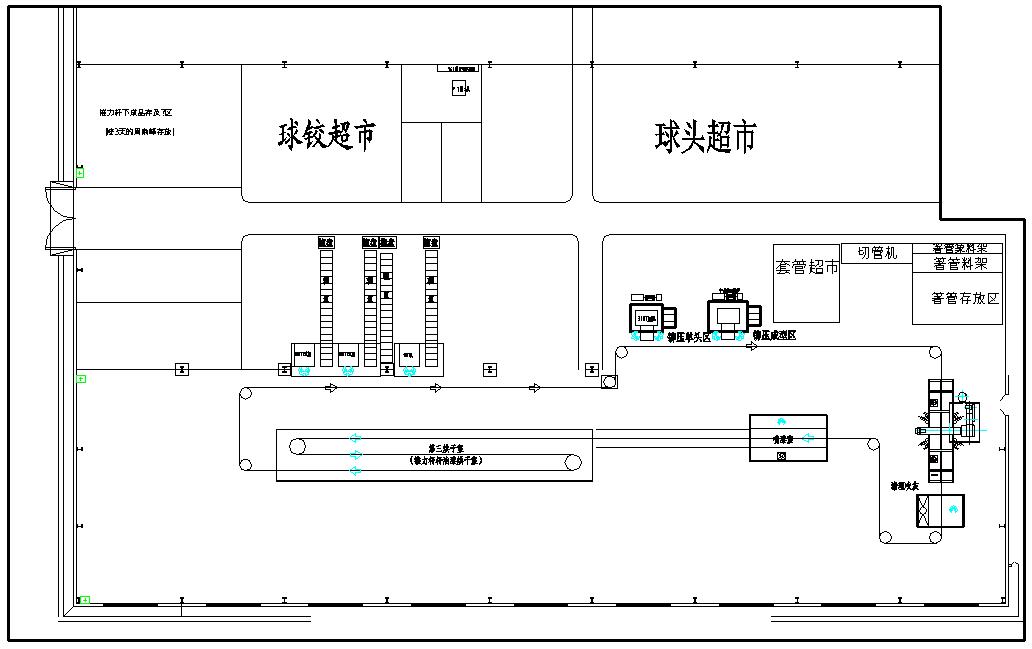
根据区域布局图结合生产情况用鱼骨图形式分析如下:
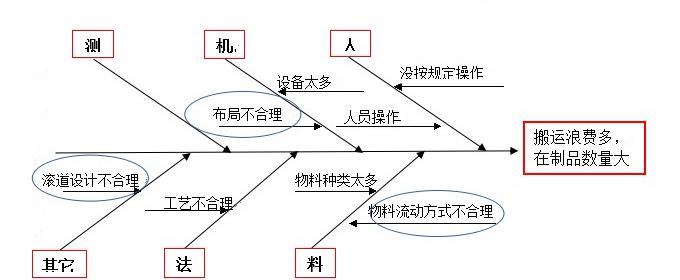
对策确定及实施
通过以上分析,根据布局优化原则,我们针对推力杆生产车间不合理方面主要进行如下改进:
①布局不合理:根据员工操作便利,对切管机位置调整和套管滚道设计;、根据最短距离原则,将球铰压装机位置调整与传送带平行。
②物流流方式不合理:在铆接工序之间,增加推力杆滚道,实现工序间物料衔接;
③滚道设计不合理:根据I/O一致节约物流空间,合理利用空间原则, 取消原有的4条滚道传送线,引进自动传送带。
具体车间布局优化调整效果图如下:
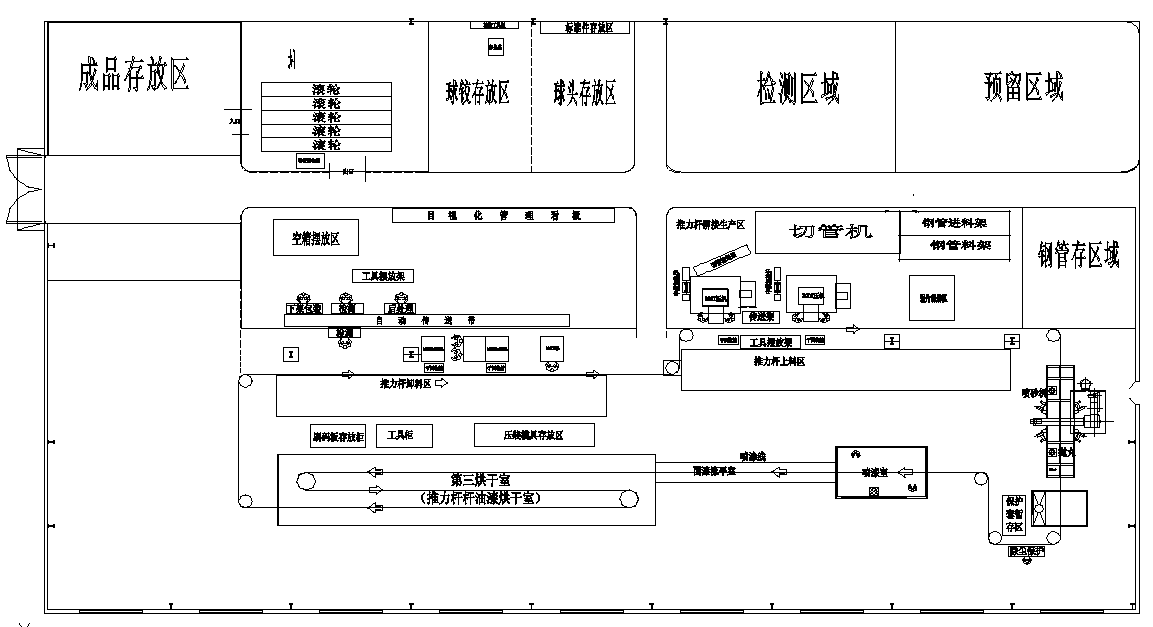
(4)综合效果
①库存方面:通过工序之间输送架的引进及设备布局调整,实现推力杆生产线的单件流生产,生产节拍控制在30S,套管在制品降为10根。
②生产周期:通过优化各工序的物流通道,减少搬运时间,使整个工序生产时间从原有349.5s降低至272.5s,生产周期缩短了77s。
③人员方面:通过对压装机位置调整及后处理自动传送带的引进,使整个工序从22人降至13人,劳动效率提高了59%。